Meet Ankit Goti: Driving Innovation at the Intersection of AI and Electronics Manufacturing
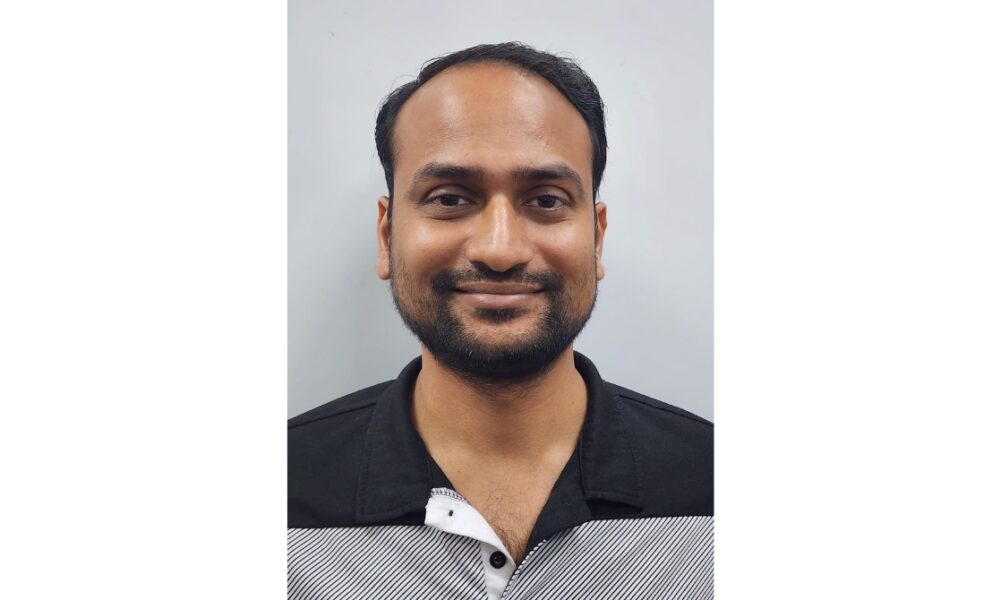
Ankit B. Goti, General Manager at HT Global Circuits, has forged a rare dual identity: seasoned manufacturing executive and forward-thinking artificial-intelligence researcher. Over the past decade he has combined hands-on experience running high-volume printed-circuit-board (PCB) plants with a rigorous program of scholarly inquiry. His résumé highlights specializations in PCB manufacturing, AI-driven reliability testing, and IPC standardization, and it notes his standing as an IEEE Senior Member and active contributor to IPC drafting committees. Together, these roles position Goti at the vanguard of Industry 4.0—where machine intelligence, data analytics, and smart automation converge on the factory floor.
Making Reliability Testing Intelligent
PCBs underpin everything from smartphones to space vehicles, and in mission-critical arenas—such as aerospace, automotive safety systems, and advanced telecommunications—failure is not an option. Traditional reliability testing relies on temperature cycling, shock and vibration trials, and painstaking microscopic inspection. While effective, these methods are slow, resource-intensive, and vulnerable to subjective judgment.
Goti’s research attacks these pain points with artificial intelligence. In a 2025 survey he mapped out how machine-learning models and physics-informed simulations can be embedded into existing IPC-9701 qualification workflows. Deep-learning–based defect detectors, trained on large image libraries, reached measured accuracies above 95 percent—far higher than conventional rule-based tools. Predictive models, meanwhile, forecast fatigue life and solder-joint failure with enough precision to slash observed field-failure rates by roughly a third.
Just as important, Goti does not gloss over the challenges. He catalogs the data-quality hurdles and high-performance-computing demands that accompany AI deployment, offers mitigation strategies, and draws a roadmap for future studies. The upshot is clear: automated, real-time reliability validation is moving from theory toward shop-floor reality.
Raising the Bar for Inspection and Quality Control
Automated Optical Inspection (AOI) has long been a staple of PCB fabrication, yet legacy AOI systems often depend on static libraries and rigid geometric rules. Goti’s work shows how next-generation AOI fuses high-resolution imaging with convolutional neural networks and adaptive learning. Comparative benchmarks reveal that AI-driven AOI pushes detection accuracy to the 98–99 percent range, while manual inspection struggles to top 90 percent. Throughput gains are similarly dramatic; intelligent AOI can assess thousands of components per hour, all while cutting false-alarm rates that force costly re-checks.
Goti further explores emerging enhancements—three-dimensional imaging for solder-volume measurement, self-training algorithms that learn from operator feedback, and seamless data feeds into factory-wide quality dashboards. Coupled with stringent IPC acceptance criteria, these innovations pave the way for near-zero-defect manufacturing.
Predictive Maintenance and Smart Process Control
Inspection is only one piece of a larger puzzle. Equipment failures, drift in process parameters, and unplanned downtime can wipe out the gains from improved test coverage. Goti therefore extends his AI toolkit to predictive maintenance and closed-loop process control. By harvesting continuous sensor streams—temperature, humidity, spindle vibration, laser power—and feeding them into algorithms such as random forests, gradient-boosted decision trees, and long short-term memory (LSTM) networks, his models detect precursor signatures of machine degradation. Maintenance can then be scheduled proactively, eliminating surprise breakdowns and maximizing overall equipment effectiveness.
In parallel, Goti advocates inserting AI “agents” into fabrication lines that dynamically tune temperature profiles, plating chemistries, and imaging exposures. The result is tighter process windows, higher yields, and faster response to environmental fluctuations.
Bridging Research and Standards
Technological breakthroughs mean little if they cannot be validated, certified, and reproduced across suppliers. Here Goti’s standards work is pivotal. As a participant in key IPC task groups, he helps draft guidelines that define how AI-based tools must be calibrated, how training data are documented, and how performance is verified. In one proposal he calls for IPC-compatible acceptance criteria for AI-enabled AOI, ensuring that algorithmic decisions are traceable and trustworthy.
By merging technical innovation with a standardization mindset, Goti addresses the twin needs of progress and reliability. Manufacturers gain clarity on regulatory expectations; customers gain confidence that AI outputs meet the same rigor historically applied to manual inspections and tests.
Alignment with Industry 4.0
The global push toward smart factories is transforming electronics production. Sensor-rich equipment, edge-to-cloud connectivity, and autonomous robots are becoming commonplace. Goti’s research fits squarely into this paradigm shift. His studies frequently focus on Class-3 PCBs destined for aerospace, defense, and medical devices—segments that demand the highest reliability bar and stand to benefit most from predictive analytics.
Technically, Goti taps the full spectrum of contemporary AI: convolutional neural networks for image recognition, generative models for synthetic-data augmentation, reinforcement learning for process optimization, and sequence models for fatigue prediction. Yet he consistently grounds these techniques in real manufacturing data and references back to IPC specifications, ensuring that academic novelty translates into production-ready tools.
Lasting Impact and Future Prospects
Across his body of work, Ankit Goti demonstrates how artificial intelligence can revolutionize a labor-intensive corner of high-tech manufacturing. Quantified improvements—defect detection rates brushing 99 percent, failure-rate reductions of a third, inspection throughputs multiplied several-fold—offer tangible value propositions for factory managers and engineers.
His forward-looking analyses point to fully automated, closed-loop validation systems. In this vision, PCBs move through lines equipped with AI guardians that inspect, predict, and adapt in real time. The human role evolves toward oversight, innovation, and exception handling rather than repetitive scrutiny.
Goti’s blend of scholarly rigor, industrial pragmatism, and standards leadership ensures that the transition to AI-driven manufacturing unfolds responsibly. By fusing domain expertise in PCB fabrication with state-of-the-art machine learning, he charts a path toward electronics that are not only smarter and cheaper to build but also more dependable in the field. As Industry 4.0 matures, his contributions illuminate how intelligent systems can think, learn, and act on the factory floor—delivering the next generation of resilient, high-performance electronic products.